Wood-based textiles are being developed in several Finnish projects ‒ huge market potential is in sight
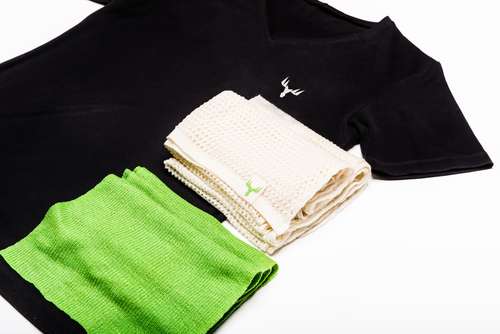
If the annual increment of Finnish forests was transformed into textiles with the technologies under development, the production would only correspond to ten percent of the world’s textile market. The same technologies can also be used in recycling textiles, which would decrease the need for virgin raw material and cotton.
Producing textiles from wood fibres is not a new thing. For example, the entire production of dissolving pulp at Stora Enso’s Uimaharju mill in eastern Finland is used to manufacture viscose.
In order to produce textiles of wood or pulp fibres, the fibres must always be dissolved. In viscose production this is done with the help of carbon disulphide.
However, carbon disulphide is highly toxic. According to Dr. Ali Harlin, Research Professor at the VTT Technical Research Centre of Finland, the main goal of the new technologies is to find a way to avoid the use of carbon disulphide.
“Carbon disulphide is a bad thing in three ways. It is toxic as it destroys neurons, in small doses it stinks and it is highly flammable,” says Harlin.
Pilot plant to produce first textile fibres in June
Of the projects under way at VTT, the farthest advanced is the carbamate process technology. In this technology, dissolving pulp is treated with urea.
In another technology, called BioCelSol, the pulp fibres are modified with enzymes. However, this technology is only about to reach a stage of determining whether it is suitable for larger-scale production.
The fibres produced in the carbamate process are soft, which makes them well suited to hygiene textiles and cotton mixtures, for example.
In fact, the carbamate technology is not a newcomer. The Finnish oil-processing company Neste already tested it 20 years ago. “At that time there was no need for the technology,” says Harlin.
“So it was shelved then, until some years ago, as a sort of students’ experiment, we used the technology to produce textile fibres from old newspapers. We found that it really worked,” he continues.
And, because carbamate technology is not a new technology, it is already well developed. “A pilot plant at VTT’s research centre Bioruukki in the Helsinki region is nearing completion. It will start producing textile staple fibres with the carbamate technology in June,” says Harlin.
The product will be commercialised by the startup company Infinited Fiber Company, and some preliminary orders have already come in. Provided that the results are good, the technology can be licensed for the first industrial-scale plant.
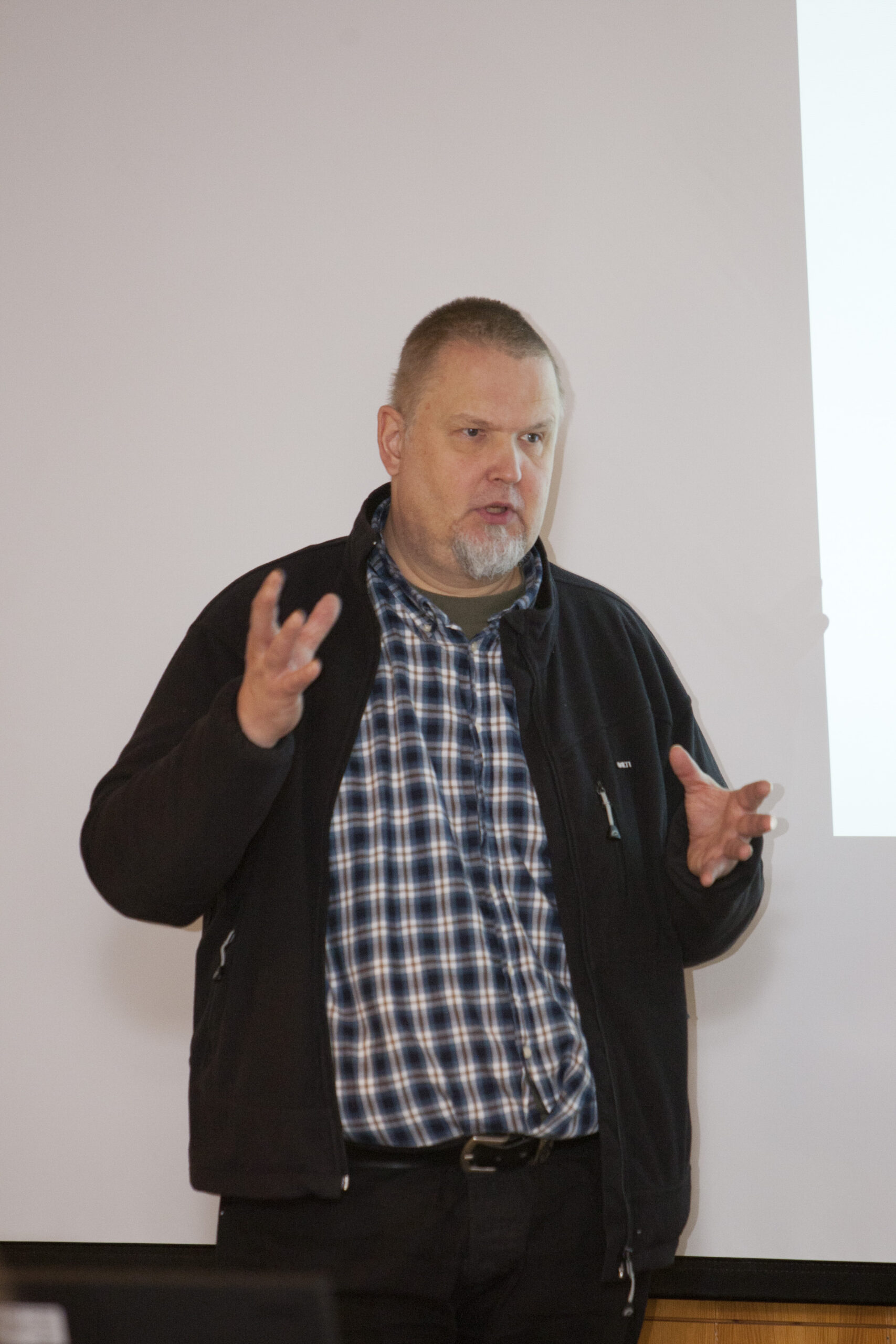
Additional EUR 1.5 million funding for Ioncell
Another technology researched by the VTT is called Ioncell-F. An advantage of the fibre produced with it is its superior strength as compared to the textile fibres sold today.
“It is produced by pulling the fibres through air using a method developed by the Aalto University. The method allows the molecular structure of the fibres to be better orientated, leading to increased tensile strength. On the other hand, the fibre is more fragile, it pills more easily and is more difficult to dye,” says Harlin.
Ioncell technology is based on an effective dissolving process using an ionized solvent developed by the University of Helsinki. The main problem in the development work is how to recover as much of the solvent as possible in order to achieve a near-closed loop circulation of the production chemicals.
The Finnish Funding Agency for Innovation Tekes recently granted EUR 1.5 million for the next development stage. For the time being, only a couple of small garments have been produced with the Ioncell technology. The next stage also aims at scaling the production up to pilot scale.
Harlin thinks it highly improbable that Ioncell could be used on an industrial scale before the late 2020s. “But it’ll definitely be a reality sooner or later,” he assures.
Yarn is also manufactured directly from wood fibres by a company called Spinnova. “You could call it a very fine paper string,” says Harlin.
Spinnova’s “paper string” is being studied from many angles, such as from the viewpoints of nanocellulose and yarn composition.
Technologies also allow recycling of textiles
The recycling of used cotton textiles is closely linked to these technologies. Large textile companies and their subcontractors are very interested in this for two reasons: the environmental problems of cotton production and the increasing amounts of textile waste.
De-dyed and cleaned cotton, such as bedsheets and towels, can be used as raw material in both the carbamate and the Ioncell process. Recycled textiles can be dissolved using the same process as for the pulp fibres.
If the production of wood fibre textiles can be profitably commercialized using these technologies, success can be guaranteed. Forest-based raw material is better in terms of its environmental impact. The cultivation of cotton creates one of the largest environmental problems in agriculture and, unlike wood fibres production, it also competes with food production for arable land.
And, compared to oil-based synthetic fibres, the production of wood fibres is more sustainable, being based on renewable raw materials. Thanks to the new technologies, the fibres are also fully recyclable.
The market is enormous
The textile markets of the world are enormous. If, for example, the total annual increment of Finnish forests was converted into textiles, it would only cover one tenth of the world’s annual textile market, which is 140–150 million metric tons.
On the other hand, the size of the world’s textile market is roughly half that of the world’s pulp market.
All tree species are suitable for the production of textile fibre. In addition to this, textile fibre has a high added value – in terms of its price per kilo, for example, textile fibre easily beats all previous bulk products of the forest industry.
Small wonder that Harlin fails to take seriously any claims that the forest industry will never again be able to develop such bulk products as magazine or copying papers. “Oh yes, it will, and with larger volumes and better prices,” he assures.
According to Harlin’s observations, the Finnish forest industry companies Metsä Fibre and Stora Enso have shown interest in the Ioncell process. Stora Enso has previously invested in dissolving pulp production at its Uimaharju mill in eastern Finland, and participates in projects of strategic research.
Metsä Fibre has already shown examples of its development work in textile production. Also, the Japanese Itochu corporation, a major player on the global textile markets, is a minority shareholder of Metsä Fibre.
At the moment the most important patents of the Ioncell process are owned by the Aalto University and the University of Helsinki. “If and when the technology begins to be scaled up to a commercially viable level, it could be done by establishing a company to demonstrate and license the technology,” speculates Harlin.
“Another option would be to sell the technology to a sufficiently large company to scale up and commercialize the production,” says Harlin.
Kirjoita kommentti